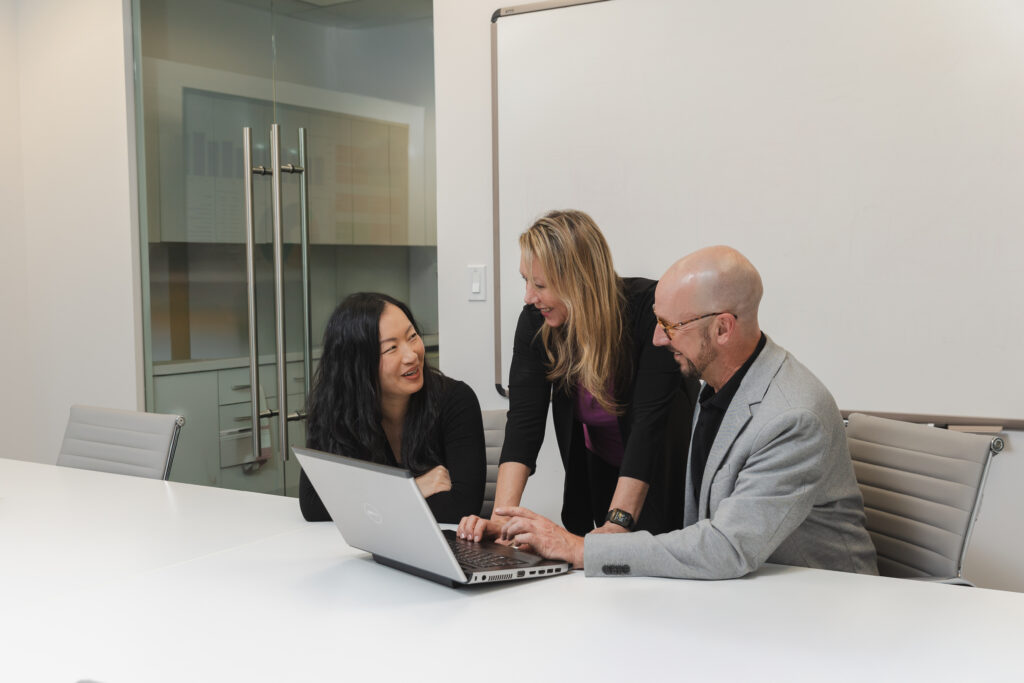
Every manufacturer understands the importance of controlling costs—whether in labor, inventory, or production. Yet, when it comes to ERP systems, proving the return on investment (ROI) can be challenging.
Some businesses hesitate, fearing implementation costs or disruptions. Others continue relying on outdated ERP systems that quietly drain profitability through inefficiencies, excess manual work, and lack of real-time visibility.
With over 300 successful Manufacturing ERP implementations, The Answer Company understands the unique challenges manufacturers face and how to drive Manufacturing ERP ROI with best practices and expert guidance.
In our recent expert-led Acumatica Manufacturing ROI webinar, we explored the nine key factors that determine ERP success for manufacturers. Whether you’re considering a new system or looking to maximize your current ERP investment, understanding these ROI-driving factors will help you make a smarter investment.
The Business Case for Manufacturing ERP ROI
Before we explore the key factors affecting ERP return on investment for manufacturing, let’s look at the numbers.
According to the Forrester Total Economic Impact™ study on Acumatica ERP for manufacturing:
- 66% ROI within three years
- $1.4 million in net present value
- 16 months payback period
These numbers aren’t theoretical—they reflect the real-world impact for manufacturers using Acumatica. This means that manufacturers who switch to Acumatica Manufacturing Edition see measurable cost savings, higher productivity, and improved inventory accuracy in just over a year.
For manufacturers struggling with manual processes, outdated scheduling tools, or disconnected financial systems, these numbers highlight the tangible financial benefits of transitioning to a modern cloud-based ERP.
9 Key Factors That Impact Manufacturing ERP ROI
1. Production Efficiency: Optimize Workflows and Reduce Downtime
The Challenge:
Many manufacturers struggle with bottlenecks, inefficient work order sequencing, and excessive downtime caused by poor production planning.
Acumatica’s Impact:
- Advanced Planning and Scheduling (APS) optimizes job sequencing based on available resources.
- Real-time shop floor data tracking ensures accurate work order execution.
- Automated workflows reduce manual tracking and approval delays.
Imagine a metal fabrication shop where production schedules are manually adjusted throughout the day. Delays stack up as workers wait for job assignments, and last-minute material shortages force urgent changes. By implementing Acumatica, the manufacturer automates job sequencing, minimizes idle time, and reduces wasted materials—leading to faster order completion and better resource utilization.
2. Inventory Optimization: Reduce Carrying Costs Without Stockouts
The Challenge:
Excess inventory ties up capital, while stock shortages delay production and frustrate customers.
Acumatica’s Impact:
- Material Requirements Planning (MRP) helps forecast demand and align purchasing.
- Real-time inventory visibility prevents over-ordering and stockouts.
- Automated replenishment ensures just-in-time material availability.
Carrying excess inventory is expensive. If a company holds $2 million in raw materials inventory and just 10% of that stock is over-purchased, that’s $200,000 in unnecessary spending. With inventory forecasting and automated replenishment, manufacturers can optimize purchasing decisions, reducing excess stock and freeing up six figures in working capital for business growth.
3. Supply Chain Optimization: Prevent Delays and Improve Vendor Performance
Supply chain inefficiencies can lead to production delays, rising costs, and missed customer deadlines. Manufacturers that lack real-time supplier tracking and automated procurement tools often struggle to respond to disruptions effectively.
With Acumatica Manufacturing Edition, manufacturers can:
- Gain real-time visibility into supplier performance to avoid costly delays.
- Automate purchase order (PO) generation to streamline procurement workflows.
- Use multi-carrier shipping and logistics tracking to improve delivery accuracy.
- Monitor key supply chain KPIs (on-time shipping, supplier costs, inventory turnover) with role-based dashboards.
By centralizing all supply chain data in one ERP system, manufacturers improve forecasting accuracy, reduce lead times, and optimize material sourcing—leading to a more resilient, cost-efficient supply chain.
4. Labor Cost Reduction – Automating Workflows for Higher Productivity
Labor costs account for a significant portion of a manufacturer’s expenses. However, many businesses lose money not due to wages alone, but because of inefficiencies in time tracking, job assignments, and manual administrative tasks. Without automation, companies face higher labor costs, lower productivity, and difficulty scaling operations efficiently.
Acumatica’s Impact:
- Automated job tracking and barcode scanning reduce manual data entry and prevent errors.
- Real-time workforce dashboards provide visibility into labor utilization and productivity metrics.
- Mobile ERP access allows employees and supervisors to update job progress from anywhere, improving response times.
- Automated approval workflows eliminate administrative bottlenecks and speed up decision-making.
Manual tracking is one of the biggest hidden costs in manufacturing. If a machine operator spends just 15 extra minutes per shift manually recording production data, at a labor rate of $25 per hour, that adds up to $6.25 per shift. Across 50 operators working two shifts per day, that’s $625 per day in lost productivity—over $16,250 per month.
By implementing real-time job tracking and automated data collection, manufacturers can trim this wasted time and reinvest those hours in higher-value production tasks.
5. Preventative Maintenance: Minimizing Downtime and Repair Costs boosts Manufacturing ERP ROI
The Challenge:
Unscheduled machine failures lead to production stoppages, emergency repairs, and increased costs.
Acumatica’s Impact:
- Automated maintenance scheduling prevents unexpected breakdowns.
- Work order tracking and asset management ensure timely repairs and part availability.
- IoT integration and predictive analytics help detect early maintenance needs before failures occur.
Unplanned machine downtime is a costly but often overlooked challenge in manufacturing. Even if it occurs just twice a month for four hours each, the impact adds up quickly. With downtime costs reaching $5,000 per hour, that’s $40,000 in lost production every month—or nearly $500,000 per year.
By leveraging advanced planning, scheduling automation, and predictive maintenance tools, manufacturers can cut downtime by 50% or more, unlocking significant cost savings and operational efficiency.
6. IT and Infrastructure Cost Savings: Reducing Total Cost of Ownership with Cloud ERP
For many manufacturers, the cost of maintaining on-premise ERP systems goes beyond the initial investment. Hidden expenses like server maintenance, IT staffing, security updates, and software upgrades can quickly add up, making it difficult to scale operations efficiently.
Transitioning to a cloud-based ERP like Acumatica helps manufacturers reduce IT costs, improve system reliability, and scale without expensive hardware investments, boosting manufacturing ERP ROI.
Acumatica’s Impact:
- Eliminates costly on-premise hardware and IT maintenance.
- Unlimited user licensing model reduces per-user software fees.
- Automated security updates and cloud backups lower cybersecurity risks.
- Seamless integrations with third-party applications reduce expensive custom development.
Many ERP providers charge $2,000 per user per year in licensing fees. For a 50-person team, that’s $100,000 annually just for user access.
With Acumatica’s unlimited user model, the same company pays a fixed subscription fee, reducing costs and allowing them to onboard more employees without increasing software expenses. Over five years, they save $500,000—money that can be reinvested into production and expansion.
7. Compliance and Quality Control: Avoiding Costly Regulatory Penalties
Manufacturers must meet strict industry regulations and maintain high product quality standards to avoid penalties, product recalls, and reputational damage. However, managing compliance manually or with disconnected systems increases risks, slows down production, and creates costly errors.
Acumatica Manufacturing Edition provides automated compliance tracking, real-time quality control, and full traceability, ensuring manufacturers meet industry standards efficiently.
Acumatica’s Impact:
- Lot and serial tracking ensures complete product traceability for recalls and audits.
- Automated quality control workflows reduce errors and improve consistency.
- Regulatory reporting tools streamline compliance with FDA, ISO, and other industry-specific standards.
- Non-conformance tracking and corrective action workflows help prevent future quality issues.
Defective products don’t just cost money—they damage customer trust. If 0.5% of all shipments require a return due to defects, and each return costs $150 in rework, shipping, and lost revenue, then a company shipping 10,000 units per month is losing $7,500 monthly, or $90,000 per year.
Automated quality control and non-conformance tracking can cut defect rates by 50% or more, reducing rework costs and improving customer satisfaction.
8. Faster, Accurate Order Fulfillment: Increasing Revenue and Customer Satisfaction
Order fulfillment delays can lead to missed sales opportunities, lost customers, and increased operational costs. Many manufacturers struggle with inefficient sales order processing, inventory inaccuracies, and disconnected fulfillment workflows, causing bottlenecks. Acumatica Manufacturing Edition automates order processing, optimizes inventory allocation, and improves warehouse efficiency to ensure on-time delivery.
Acumatica’s Impact:
- Automated sales order processing reduces manual errors and accelerates fulfillment.
- Warehouse Management System (WMS) integration improves picking and packing accuracy.
- Real-time inventory visibility prevents backorders and stock shortages.
- Multi-location fulfillment support optimizes shipping and reduces lead times.
A 5% error rate in order fulfillment can have a significant financial impact. If a manufacturer processes 500 orders per week with an average order value of $2,000, a 5% error rate results in 25 incorrect shipments per week, a potential loss of up to $200,000 in lost revenue monthly. Automated order tracking and warehouse management systems can cut fulfillment errors by 75%, recovering up to $1,800,000 annually in lost sales and customer churn.
9. Business Intelligence: Data-Driven Decision-Making for Maximum Manufacturing ERP ROI
Manufacturers today generate vast amounts of data—but without the right ERP system, this data often remains siloed in spreadsheets, disconnected software, or outdated reporting tools. This leads to slow decision-making, inaccurate forecasting, and missed opportunities. Acumatica transforms manufacturing data into a real-time strategic asset, helping leaders make informed, data-driven decisions.
Without real-time analytics and role-based dashboards, executives and managers struggle to monitor performance, leading to inefficiencies across departments. Acumatica’s built-in business intelligence tools provide real-time visibility into financials, operations, and supply chain performance, enabling proactive decision-making.
Acumatica’s Impact:
- Role-based dashboards provide instant access to financial and operational KPIs.
- Predictive analytics and AI-driven insights improve demand planning and cost control.
- Automated reporting tools reduce reliance on manual data compilation and errors.
- Real-time access to profitability, cost trends, and sales performance supports strategic growth.
Manually compiling financial reports is a hidden cost for many manufacturers. If a finance team spends 40 hours per month gathering data across multiple systems at an average salary of $50 per hour, that’s $2,000 in lost time per month, or $24,000 per year. With real-time dashboards and automated reporting, manufacturers can eliminate manual reporting tasks and reallocate resources to higher-value financial analysis.
Related Resources
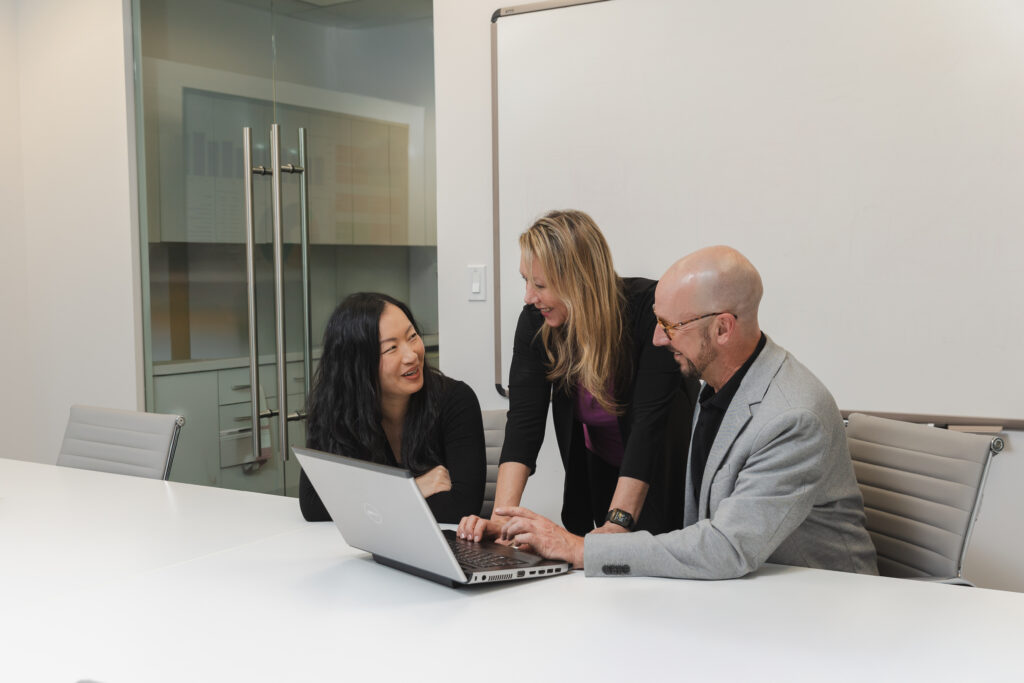
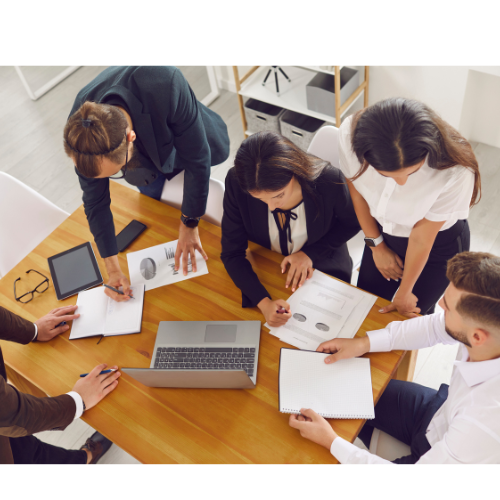
Maximize Visibility with Acumatica Dashboards: Custom Tips, Tricks & Real-World Use Cases
Read the Article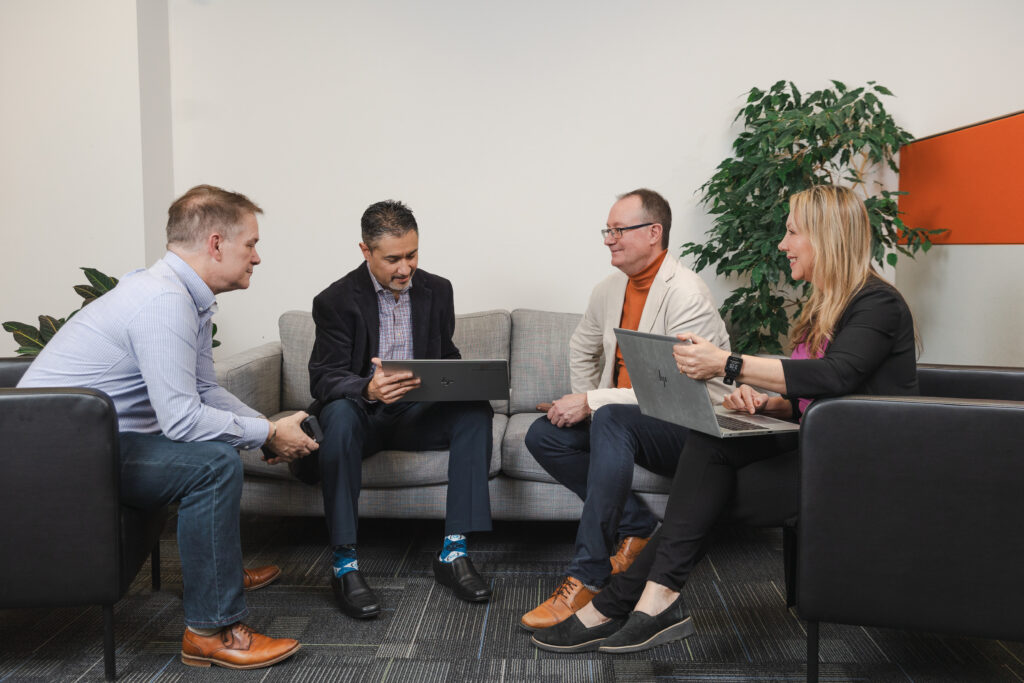